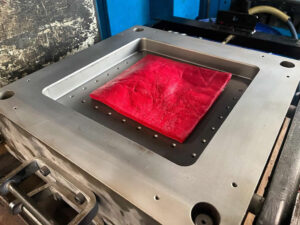
With 60 years of experience in the rubber moulding industry, we have earned a reputation for manufacturing top quality products and providing exceptional customer service. Whatever industry you are in, whether it is automotive, aerospace, agriculture, or any other sector, we have the expertise to meet your needs.
Rubber transfer moulding is a versatile manufacturing process used to produce precision rubber components with excellent dimensional stability and intricate designs. This process involves transferring pre-measured amounts of rubber material into a heated mould cavity under pressure, resulting in consistent and uniform parts with minimal wastage.
Here’s how the process works:
- Material Preparation:
The rubber material, usually in sheet form is cut to the appropriate size using a slitter table or guillotine. Alternatively the material can come in preformed blanks which are extruded and cut to length and size. The rubber is then weighed out to a predetermined amount ready for loading into the transfer pot. - Loading the Material:
In transfer moulding, the rubber material is loaded into a chamber called the pot or transfer chamber located below the mould cavity. This chamber is equipped with a piston that will apply pressure and transfer the material into the mould cavity. - Heating:
The mould and the rubber material are heated to a specified temperature to soften the rubber and facilitate the moulding process. The temperature and heating duration are carefully controlled to ensure proper flow and curing of the rubber. - Transfer and Compression:
The piston applies pressure to transfer the material from the pot into the mould cavity. The rubber flows through channels or runners (sprues) into the cavity, filling it completely. - Curing:
After the mould cavity is filled with the rubber material, the entire mould assembly is subjected to heat and pressure to cure the rubber. Curing involves cross-linking the polymer chains within the rubber compound, resulting in the formation of a stable and durable rubber product. - De-moulding:
Once the curing process is complete, the mould is opened, and the finished rubber product is removed from the mould cavity. Any excess material, known as flash is removed from the mould ready to start the process over again. The product will receive a primary quality check then set aside too cool. - Finishing procedures:
Depending on the specific requirements of the product, additional post-processing steps such as surface finishing, trimming and secondary quality check will be performed, to ensure the final product meets the desired specifications and standards before being shipped to the client.
Why Choose Our Rubber Transfer Moulding?
- Precision Engineering: We work closely with our UK based toolmakers to meet the most stringent specifications and tolerances.
- Custom Solutions: Whether you need simple gaskets or intricate mouldings, we can utilise our transfer moulding processes to suit your specific requirements. From design assistance to material selection, we work closely with you to deliver exactly what your product requirements are.
- High-Quality Materials: We use the highest quality rubber materials from our trusted suppliers, ensuring durability, resilience, consistency and excellent product performance. Our comprehensive material selection includes Silicone, EPDM, Neoprene, Natural, Nitrile, FDA compounds and more.
- Fast Turnaround Times: We understand the importance of timely delivery. With our efficient manufacturing processes and streamlined workflows, we can meet even the tightest deadlines without compromising on quality.
- Cost-Effective Solutions: Our rubber transfer moulding services offer a cost-effective solution, for producing large quantities of rubber components with consistent quality and minimal waste, helping you save time and money in the long run.
Our free quoting process is simple and efficient. Call us: +44(0)1406 330467 or Email us: webenquiry@wjwebb.co.uk to discuss your transfer moulding requirements, send us a sketch or a drawing along with any specific requirements and we will do the rest!