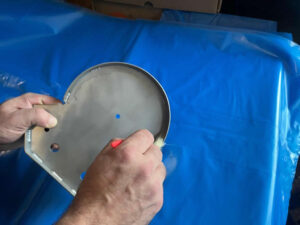
Rubber to metal bonding during the vulcanisation stage is a common process used in various industries, ranging from automotive to manufacturing. This method creates a strong and durable bond between the rubber component and metal substrate, providing resilience, flexibility, and stability in diverse applications.
The vulcanization process plays a crucial role enhancing the adhesion between the rubber compound and the metal substrate. This results in seamless integration between the rubber and metal components, by bonding them together on a molecular level. Vulcanised rubber bonding offers numerous advantages, including improved structural integrity, enhanced vibration damping, and resistance to environmental factors. By understanding the principles and technical aspects of this process, we produce high-quality bonded assemblies for a wide range of applications.
Here’s how the process works:
- Surface Preparation:
The metal substrate needs to be thoroughly cleaned to ensure optimal adhesion. This can involve degreasing, sandblasting, or chemical treatment to remove contaminants from the surface to aid bonding. - Application of Adhesive:
A bonding agent or adhesive is applied to the prepared metal surface. Usually consisting of a single laminate or a primer and top coat leaving a uniform coverage. - Loading the Mould:
The prepared metal plates or inserts are loaded into the mould, followed by a pre-determined amount of rubber. The mould is then closed up and placed into the press. - Applying Heat and Pressure:
Heat and pressure soften the compound allowing it to flow around the cavity, forcing the compound into all the contours of the mould and the curing begins. - Curing:
After a pre-set duration, the rubber compound cures and forms a strong molecular bond with both the adhesive layer and the metal substrate. and is ready to be de-moulded. - De-moulding:
After curing is complete the mould is opened up revealing the newly bonded part ready to be removed. This may be with the use of ejector pins or special tooling. The part receives a primary quality check before being set aside to cool. - Finishing Procedures:
Most parts will need any unwanted flash removing from the moulding, this trimming will be done along with a secondary quality check before being shipped to the client.
Why Choose Our Rubber To Metal Bonding Moulding?
- Precision Engineering: We work closely with our UK based toolmakers to meet the most stringent specifications and tolerances.
- Custom Solutions: Whether you need simple mountings or more complex encapsulated bonded parts, our experienced technicians work with you to ensure a strong and durable bonds, whatever the materials and substrates. We can bond all kinds metals and plastics to a variety of rubber compounds.
- High-Quality Materials: We use the highest quality chemicals and rubber materials from our trusted suppliers, ensuring durability, resilience, consistency and excellent product performance. Our comprehensive material selection includes Silicone, EPDM, Neoprene, Natural, Nitrile, FDA compounds and more.
- Fast Turnaround Times: We understand the importance of a timely delivery. With our efficient manufacturing processes and streamlined workflows, we can meet even the tightest deadlines without compromising on quality.
- Cost-Effective Solutions: Our rubber to metal bonding moulding services offer a cost-effective solution, for producing bonded rubber components with consistent quality.
Our free quoting process is simple and efficient. Call us: +44(0)1406 330467 or Email us: webenquiry@wjwebb.co.uk to discuss your rubber to metal bonding requirements, send us a sketch or a drawing along with any specific requirements and we will do the rest!