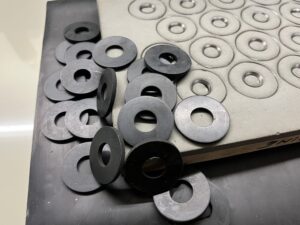
At W J Webb, we specialise in providing top quality punched materials, predominantly rubber tailored to meet the unique needs of various industries.
Our swing arm clicker press machinery ensures unparalleled accuracy and consistency in every profile cut, delivering flawlessly shaped rubber profiles that adhere to the highest standards of quality. Whether you require intricate shapes or standardised designs, our die cutting process guarantees precise results, time after time.
With decades of experience in the die cutting field, we understand the diverse applications of rubber materials across industries such as automotive, aerospace, communications, and the food industry. From gaskets and seals to custom components, our die cut rubber profiles offer accuracy and superior performance, meeting the demands of even the most challenging environments.
Our team works closely with you the client to discuss a comprehensive range of customization options, including material selection, thickness, size and design specifications, to ensure that every product aligns perfectly with your requirements, offering tailored cutting die solutions that optimize efficiency and minimize waste.
Swing Arm Clicker Press
A swing arm press (or ‘clicker press’) is used to produce gaskets or washers of any design using a cutting die. This can be a cost effective way of producing flat rubber parts from sheet material, and is fully adjustable to suit any thickness of material.
Here’s how the process works:
- Material Preparation:
Sheets or rolls of the selected rubber material are prepared for the die cutting process. This includes cleaning the material and checking it for defects before cutting it up into manageable pieces for working. - Die Setup:
The die is mounted onto a clicker press. The press is adjusted to the correct settings for the specific material and thickness being used. - Positioning:
The rubber material is placed onto the cutting bed of the die cutting machine, ensuring it is positioned accurately beneath the die. - Cutting:
The clicker press is activated and applies pressure to the die. The sharp edges of the die penetrate through the rubber material, cutting it into the desired profile. - Ejection:
Once the cutting process is complete, the die is lifted, and the newly formed rubber components are ejected from the cutting bed, usually by the aid of foam ejection housed within the die. - Inspection:
The cut rubber components are inspected for quality and accuracy. Any defects or irregularities are identified and removed. - Finishing:
Depending on the application, additional finishing processes may be required, such as removing excess material, applying adhesive backing, or adding surface treatments. - Packaging:
The finished rubber components are then quality checked, prepared for further assembly or packaged for shipping.
Why choose our rubber die cutting products?
- Precision: Our die cutting process ensures precise and accurate cutting of rubber materials, resulting in components that meet tight tolerances at your exact specifications.
- Customisation: We offer customisation options to tailor rubber components to your specific needs, including shape, size, material, and thickness, allowing for the creation of bespoke solutions.
- Efficiency: Rubber die cutting allows for high-speed production with consistent results, minimizing production time and maximizing efficiency in your manufacturing process.
- Versatility: Our die cutting services can be applied to a wide range of rubber materials, including natural rubber, synthetic rubber, silicone, FDA approved and more, accommodating various applications and industries.
- Cost-effectiveness: By optimizing material usage and minimizing waste, our die cutting services help you reduce overall production costs while maintaining quality and performance.
- Quality Assurance: We adhere to strict quality control measures throughout the die cutting process, ensuring that every rubber component meets our high standards for durability, reliability, and performance.
- Expertise: With years of experience in the industry, our team of experts possesses the knowledge and skills to tackle even the most complex die cutting projects, providing valuable insights and recommendations to optimize your designs and processes.
- Quick Turnaround: We understand the importance of meeting deadlines, which is why we prioritize quick turnaround times for our die cutting services, helping you stay on schedule and maintain productivity.
Our free quoting process is simple and efficient. Call us: +44(0)1406 330467 or Email us: webenquiry@wjwebb.co.uk to discuss your swing arm clicker press requirements, send us a sketch or a drawing along with any specific requirements and we can do the rest!