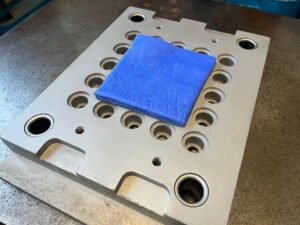
We specialise in providing top quality compression rubber mouldings tailored to meet the unique needs of our clients. With years of expertise in the industry, we take pride in offering high-quality products that exceed expectations and deliver unmatched performance.
We work closely with our clients to produce the best, most efficient and accurate moulds to their specified tolerances, by making single or multi-cavity tools from tooling-grade aluminium’s to P20 grade steel for production tooling.
Compression moulding is a manufacturing process used to produce a variety of rubber components from grommets and O-rings to engine mountings and sporting equipment.
Here’s how the process works:
- Preparation of Material: The process begins with the preparation of raw material, usually in sheet form or preformed blanks. The material may be natural rubber, synthetic rubber, or custom rubber compounds tailored to specific specifications.
- Loading the Material: The prepared rubber material is placed into an open mould cavity, which is made of steel or aluminium. The amount of material loaded into the mould is pre-cut and weighed based on the desired size and shape of the final part.
- Closing the Mould: Once the material is loaded into the mould, the mould is then closed using hydraulic pressure. This creates a closed cavity with the rubber inside, ready for compression.
- Applying Heat and Pressure: Heat and pressure are applied to the closing or closed mould to start the compression moulding process. Heat softens the rubber, making it more pliable and allowing it to flow around the mould cavity. The pressure applied compresses the rubber, forcing it to fill all the contours of the mould.
- Curing: After the material has been compressed and formed into the desired shape, it undergoes a curing process to solidify and set. The curing process involves heating the mould to a specific temperature for a set period of time, this allows the rubber to cross-link and cure.
- De-moulding: After curing is complete, the mould is opened, and the newly formed rubber part is removed. This de-moulding step may require the use of ejector pins or other mechanisms to release the part from the mould. The new part has a primary quality check, then is allowed to cool before handling.
- Finishing procedures: Most parts will need the flash removing from the moulding, this trimming will be done along with a secondary quality check before being shipped to the client.
Why Choose Compression Rubber Moulding?
- Versatility: Compression rubber moulding can produce complex shapes with intricate details, making it suitable for all sorts of applications across various industries.
- Cost-Effectiveness: Compression moulding is a cost-effective solution for both prototyping or high-volume production. With lower tooling costs and shorter production cycles compared to other methods.
- Material Compatibility: This process can be used for a wide range of rubber materials, including natural rubbers, synthetic, silicone, and speciality rubber including FDA approved (food-safe), non-bloom, or non-conductive compounds, allowing for flexibility in material selection.
- Consistency and Quality: Rubber compression moulding ensures even material distribution and part consistency, producing high-quality components with excellent performance and durability.
- Customization: We offer custom compression rubber moulding solutions tailored to your specifications, including overall part design, material selection, and finishing options, to meet your unique needs and requirements.
Our free quoting process is simple and efficient. Call us: +44(0)1406 330467 or Email us: webenquiry@wjwebb.co.uk to discuss your compression moulding requirements, send us a sketch or a drawing along with any specific requirements and we will do the rest!